- Strona główna
- -
- Aktualności
- -
- Case study: Transsystem for Continental Kaluga in Russia
Case study: Transsystem for Continental Kaluga in Russia

Our specialists were responsible for developing and implementing a solution to increase the production of studded winter tyres (spikes). This type of tyre is particularly popular in Scandinavia and Russia. The tasks of Transsystem’s engineers included meticulous measurements, designing a layout, writing software and then readying it for production in a factory in Kaluga. In addition, after the launch, through remote access to this system, the company’s team was able to support the client „on the spot” and make the necessary modifications and optimization remotely. The result? Launching the production of winter tires on the second „Spiking Loop” line, allowed to increase the production by 1,440 units per hour.
The project started in August 2018 and continued until mid-January 2019. Its timeline included:
A trip to Kaluga
The first stage was a trip to the factory to conduct an audit, which in this case was quite a difficult process as it required, among other things, that Transsystem’s specialists be granted visas.
Note: An audit is conducted at the initial stage of a project, when Transsystem sends a team of specialists to a prospective customer’s factory: steelwork and mechanical engineers, safety specialists (responsible, for among other things, the design and installation of safety solutions, which prevents dangerous accidents), an electrical engineer, and a software developer who is responsible for choosing the optimal solution, drives, inverters and efficient design of the control system. Transsystem specialists review the customer’s infrastructure, identify business needs, and make detailed measurements. This allows for the determination of the types of conveyors for the transport system necessary for each stage of the line. In addition to technical aspects, the Transsystem’s team obtain information on the efficiency of the machines used, production capabilities, the number of tires produced and the length of all other operational times.
Learning about the client’s needs
Back in Russia, the Transsystem team met with Continental’s engineers to discuss the details of the project and to get to know their needs. This allowed them to create the layout for production, the most important part of the project.
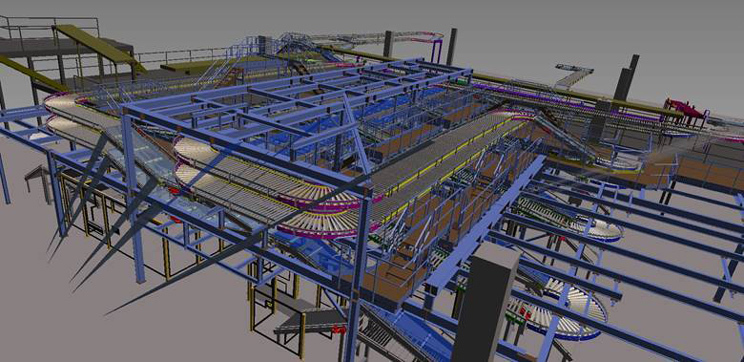
Going remote
Then, the work on the Continental Kaluga project, including the fine-tuning of details, was done online. The next step was implementation. We selected the types of conveyors and their lengths, adjusted the interlocks and made buffers.
Note: A buffer is necessary when a machine has downtime or suffers a breakdown, so that there is not an excess number of tyres directed to a particular machine – tyres have to go to a ‘buffer line’ or a ‘hospital line’ and wait for machine recommencement.
Teamwork is a key to success
Due to the complex scope of the project, all of the company’s teams participated in it. Transsystem’s advantage, once again, turned out to be an integrated team of specialists with access to information at every stage of the project, making it possible to provide the client with the highest quality solution in a very short space of time. Cooperating with Continental Kaluga included:
Mechanical engineers. They play the most important role in a project: they analyse the entire mechanical layout, work out the exact routing of the tyre transport, design all of the equipment and prepare the production documentation. All other specialists are dependent on this team’s work.
Steelwork engineers. Once the layout has been approved, they determine where steel structure supports should be placed, and check if there are any potential issues with forklift trucks or people’s working paths. The aim is to fit the design into the factory’s existing processes.
Software developers. They prepare the project by planning the layout of sensors, control cabinets and cabling as well as the programming logic of the complete line.
A dedicated project manager who controls the project time-schedule, budget and is responsible for updating the client.
Fitters (mechanical / electrical). They have the greatest impact on the customer’s opinion about the company (after all, they go to the site and build the system). They must be reliable, resourceful, accurate, and anticipate as well as react to potential design errors to avoid project delays.
Challenges
The biggest challenge was the implementation schedule at the Continental factory, which had to take place in just 3-4 weeks in late December/early January, due to the disruption with existing systems and the factory’s planned seasonal production shutdown. As a consequence, the project had to be carried out during the Christmas production break so that the factory could then operate normally afterwards. Any potential disruptions were eliminated by modifying or dismantling the existing steel structures, which was made possible by an audit carried out during the first stage of the project.
An additional challenge was of course transportation to Russia (due to complex customs and tax procedures), as the entire ten-truck convoy had to arrive at the factory complete and on time. In addition, using a local assembly company was another challenge. However, the Transsystem specialists provided supervision of the assembly, and thanks to the appropriately planned logistics of the project, it was completed on time.
Precision is what matters
Our company assumes that an individual approach to each project increases its chances of success. In the case of our cooperation with Continental, the main advantage of the Transsystem solution was that the layout and types of transport conveyors used were ascertained after technical discussions with engineers at the Kaluga factory. In addition, the system had to be equipped with new platforms that had to be connected to existing infrastructure. It was therefore necessary to take detailed measurements at the factory before starting the design, due to the presence of many issues with existing systems and platforms.
Transsystem specializes in designing and manufacturing material handling systems suited to the needs of its customers. The company has gained experience by implementing projects in many countries, in the vast majority of tire and car factories around the world as well as other industrial sectors.
If you want to discuss what solutions would be the best for your company, contact us: https://new.transsystem.pl/en/contact/
To learn more about Transsystem’s offer, please go to: https://new.transsystem.pl/en/offer/transportation-of-tires-wheels-and-rims/
Read more: new.transsystem.pl/en/news/why-the-tire-industry-needs-a-specialized-handling-systems-suplier